As “Made in Japan” products are being reevaluated, we now often see the words “production area” as well. Each area has its own culture, climate, and history, unique characteristics without which it would not have become a producer.
Here, we will trace POLS’s production in the Banshu production area, located in Hyogo prefecture, the production epicenter of yarn-dyed textiles. POLS is a factory-label established by MARUMAN Inc., a local textile trader in Nishiwaki City, Hyogo Prefecture. It is connected with the KAJIHARA DESIGN STUDIO, led by textile designer Kanako Kajihara, who has dedicated herself to rekindling the values of the work done by traditional Japanese textile mills.
The centre of Banshu-ori textiles, Nishiwaki City, is in the north of Kobe City. It is located in the so-called “centre of Japan,” where the 135 degrees east longitude and the northern latitude of 35 degrees cross.
Nishiwaki is surrounded by mountains in all directions. There are two rivers in the city, which come together in the shape of a Y; the downtown was formed where the two rivers meet. The water from these rivers assisted in the development of many industries in this area, including Banshu-ori textiles.
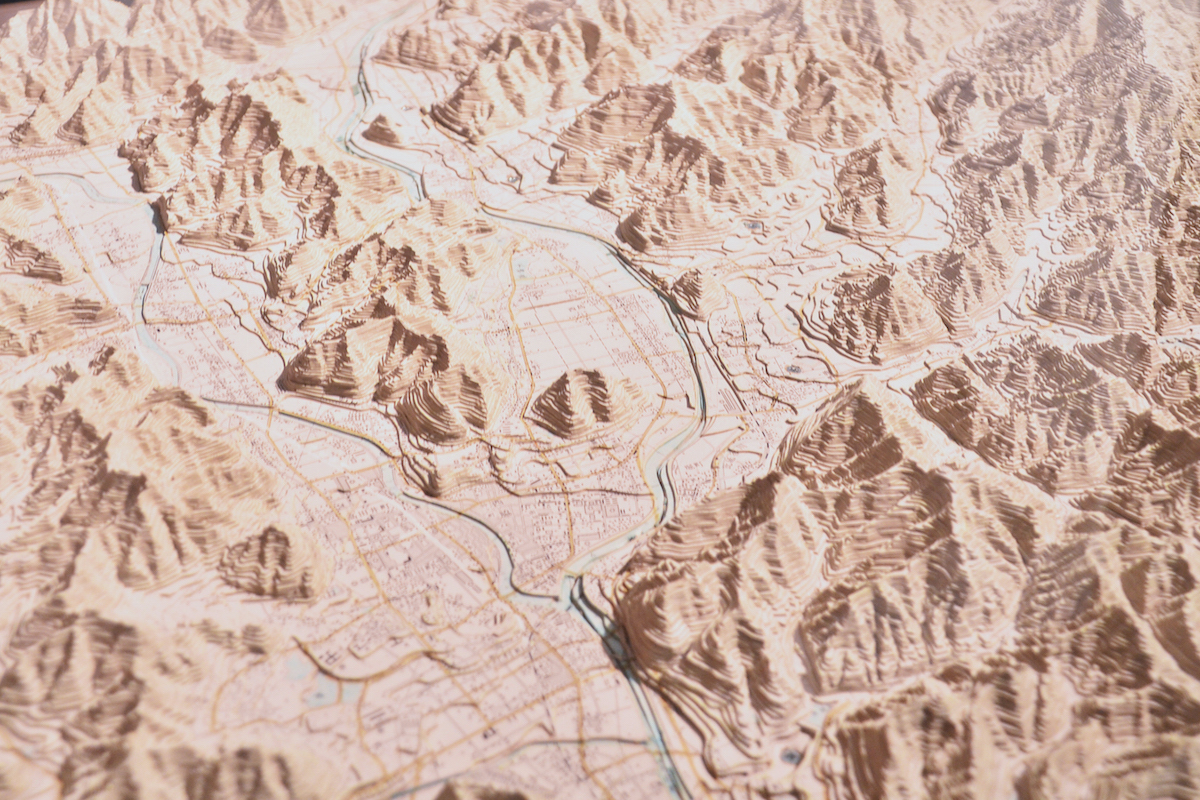
Diorama of Nishiwaki City. The rivers come together in the shape of Y.
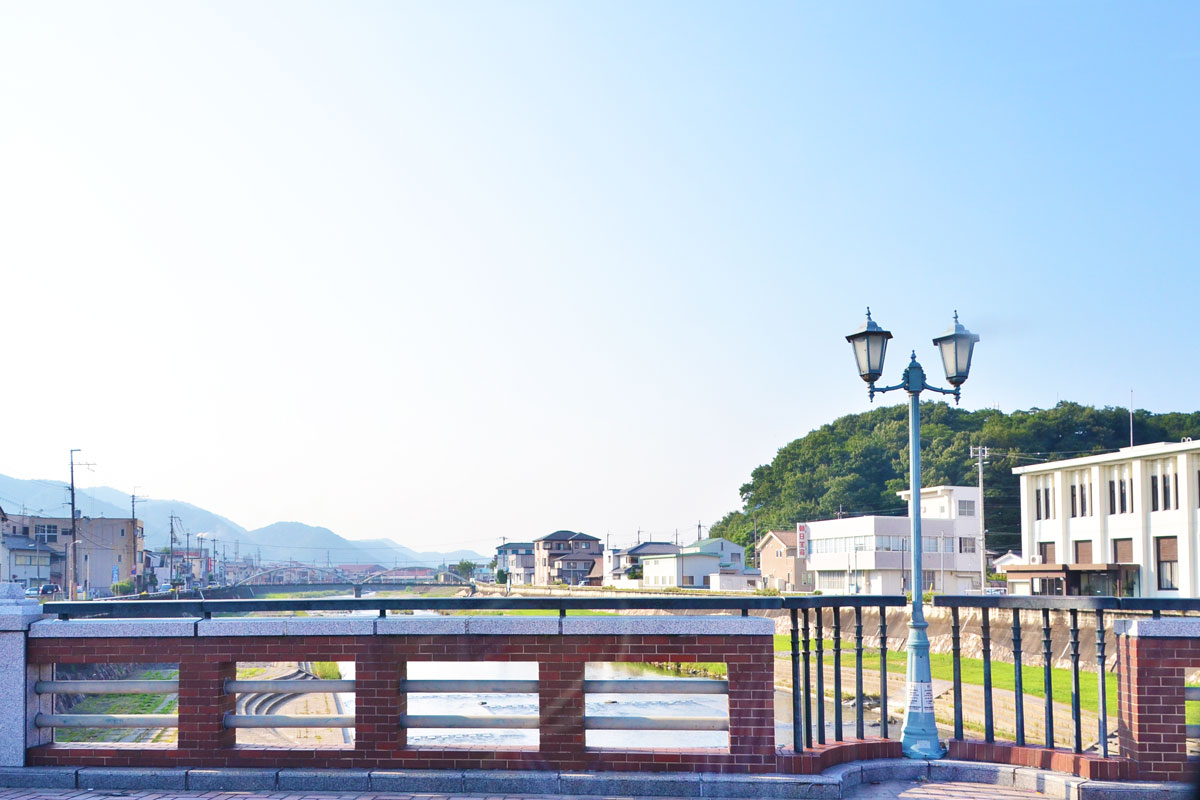
View from one of the rivers; Kakogawa River.
Rivers: An Indispensable Water Source
Many small streams from mountains join the main river in the northern area of Banshu, which is the old name of the region that includes Nishiwaki. These streams have very soft water, which was one of the factors underlying the development of the dyeing industry here. In the late 19th century to the 1930s, people used to wash yarns in these rivers, which they dyed or bleached.
Even now, the Muratoku Dyeing Company uses the water from this river to dye their yarns. They employ around 2000 tons of water from the rivers and sub-soil. They process the water to meet the standard of the Special Law on Seto Inland Sea Environmental Conservation, then return it to the sea.

Inside the Muratoku Dyeing Company is very warm.
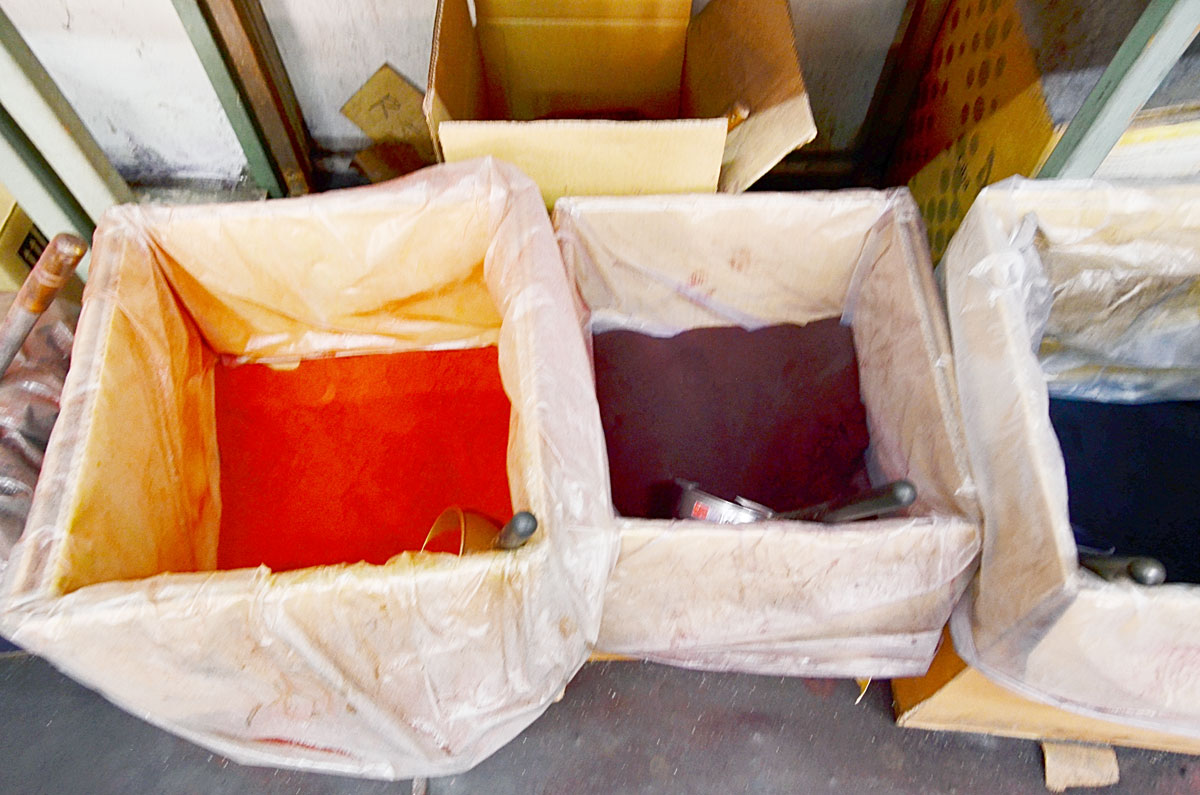
synthetic dyes at Muratoku Dyeing Company. Marutoku recycles the used water into fertilizer.
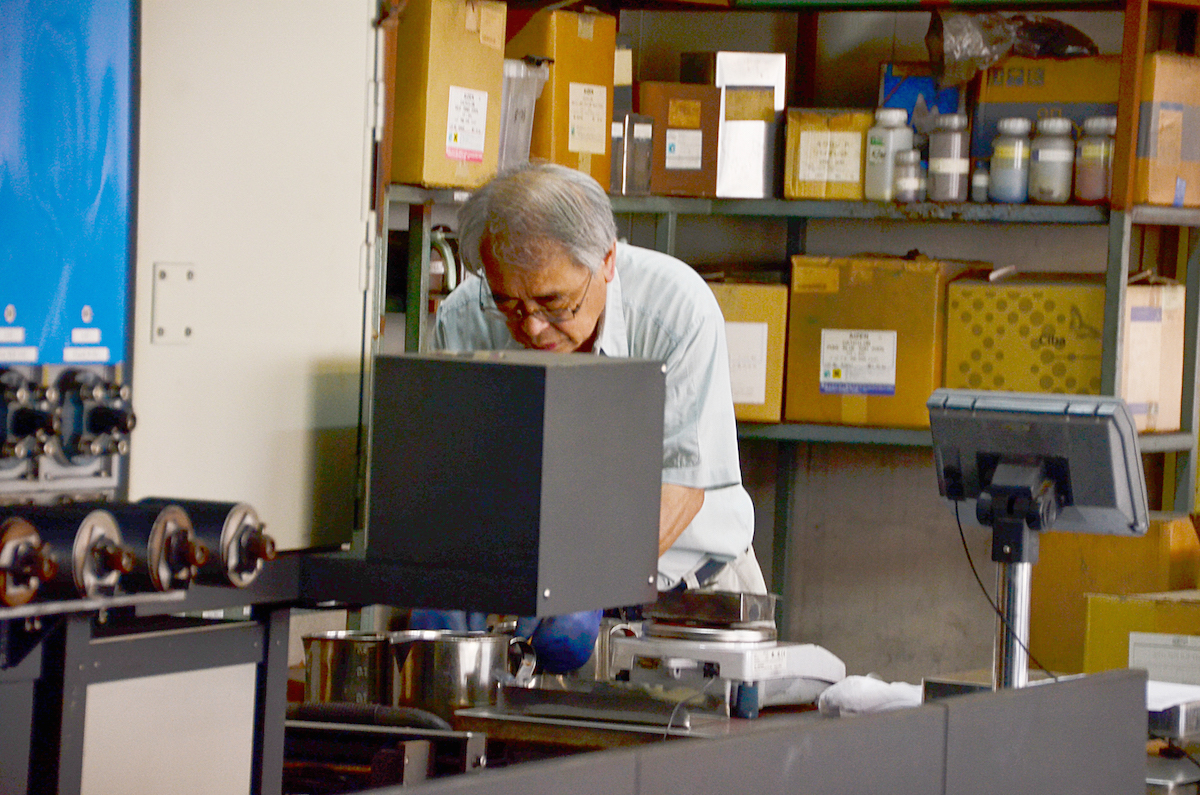
Engineers with skilled sense measures and blend the dyes that is too little to be done by machine.
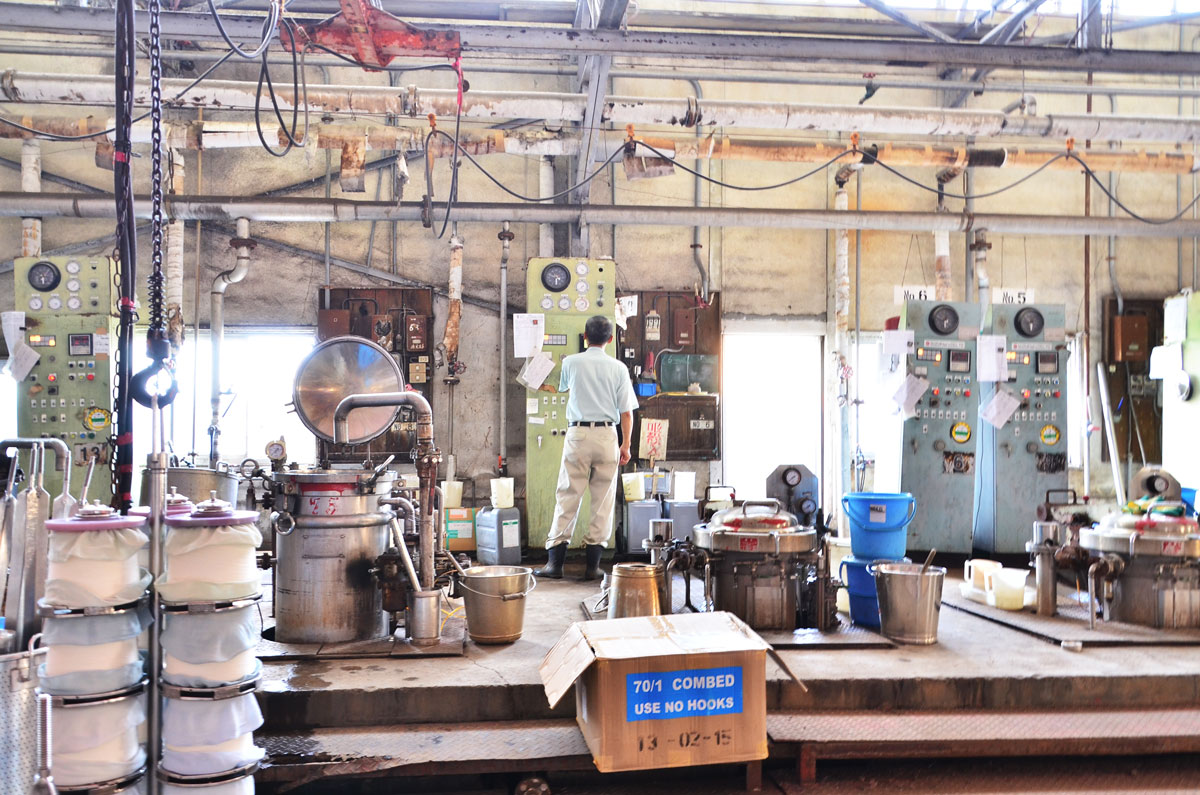
There used to be 170people working at Marutoku. Now, 30 remains.
Water is also indispensable in the final adjusting process of the woven textile. For this process, the Banshu-ori Textile Industry Co-Operation uses 1000 tons of water per day. Factory director Hirohito Matsuda says, “It will be a serious problem if we run out of water, so we have a signal for the well.” The signal turns yellow and red as the water decreases.
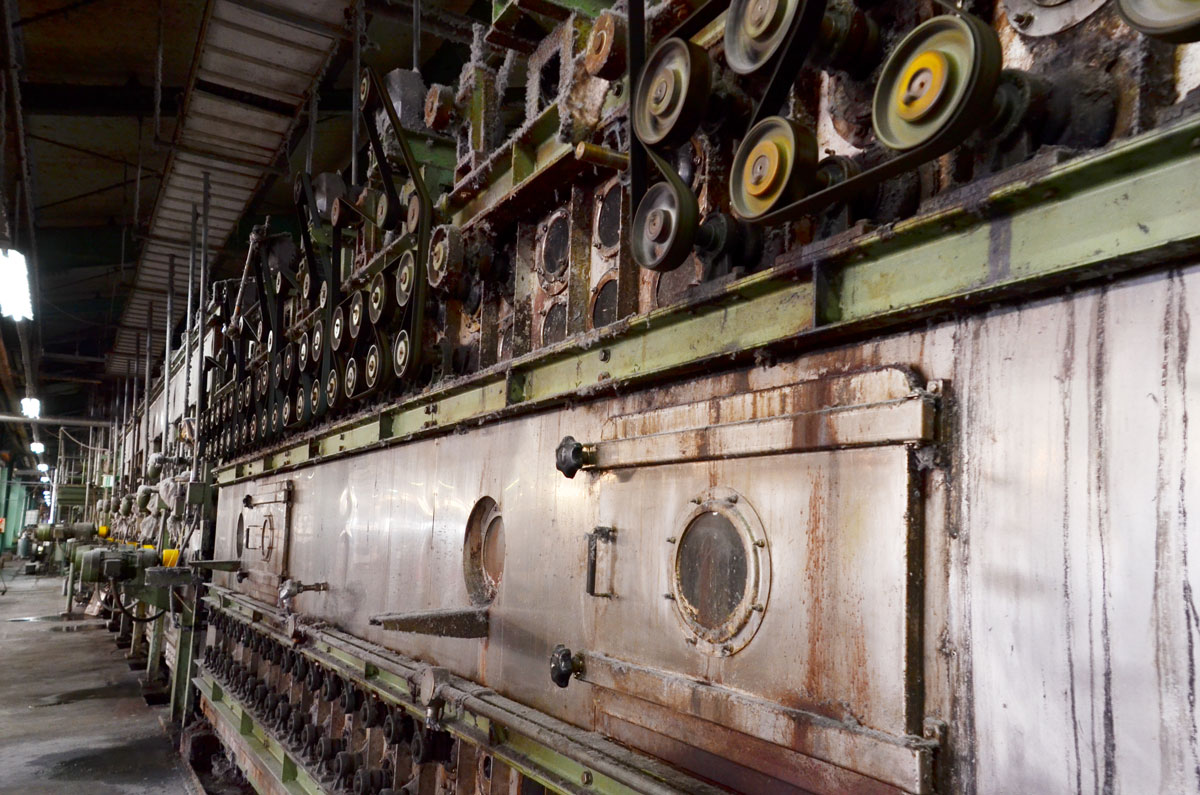
Flowing down the long lane, final touches are applied to the textile.
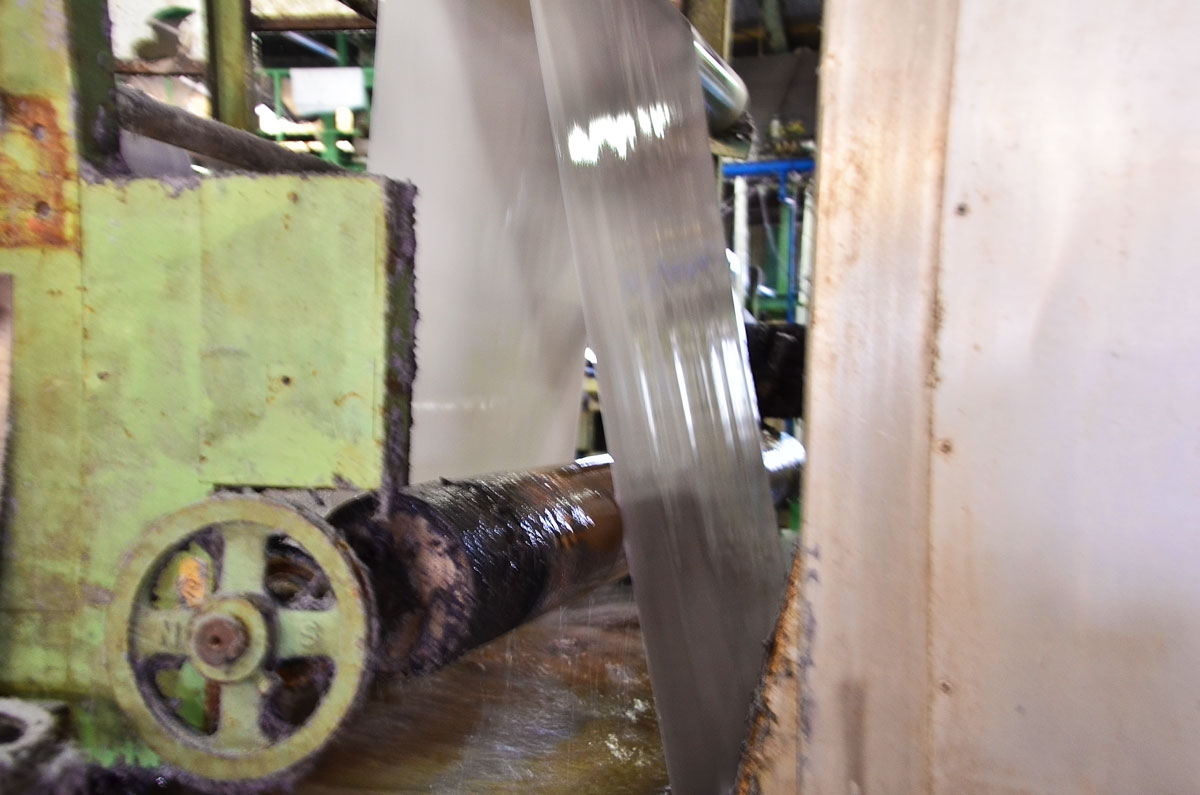
Textiles are soaked, washed and dried for numerous times to add values, such as UV-cut, deodorant-resistant, raised fiber etc.
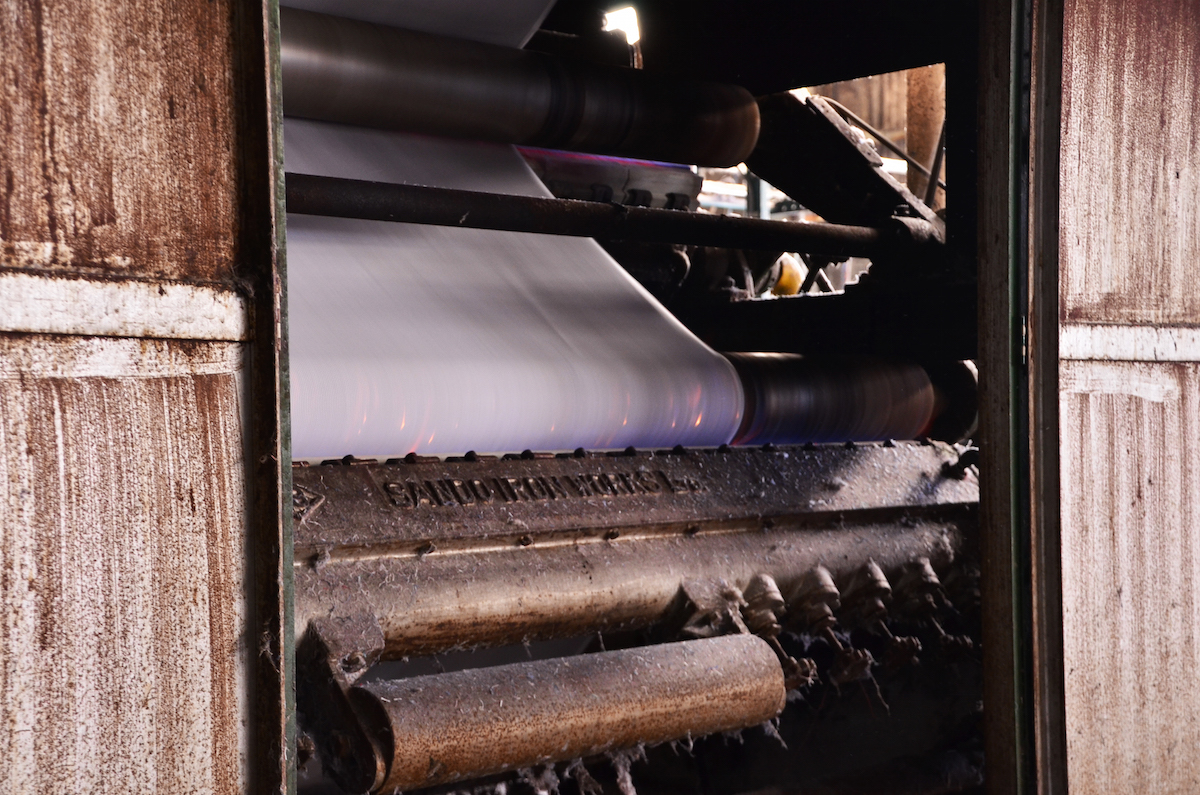
You may see the sparks burning the surface of the texitle.
Warm Climate Near Kyoto
In Banshu, people started growing cotton in the 18th Century as its warm climate was suitable for plantations. Once the technique of Nishijin, a style of weaving using various colors of silk yarns woven to make patterns, was introduced from Kyoto, they developed it into the Banshu weaving style, using cotton.
Now they are famous for yarn dyed weaving, a process in which they first dye yarns, then weave them into all sorts of patterns (as opposed to piece dyeing, in which printing is done on woven textiles). By changing the number, thickness, and colors of yarns used on warp and weft, there are countless possibilities of patterns available. POLS’ most defining characteristic is that it combines numerous weaving techniques.
Using the latest computer Jacquard technology, you can create patterns as if they were printed. For example, by changing the thickness and the number of yarns, they adjust the way the colors look. By cutting the weft fractionally, it produces motifs with a patchwork-like look. POLS uses these various techniques and offers many facets in just one textile.
Even if you understand the logic, you also have to understand the structuring in order to realize the pattern. Ueda Yoshinori from Maruman is in charge of structure design, and partners with Yoshitaka Endo Enmago Weaving Corporation for the actual weaving.
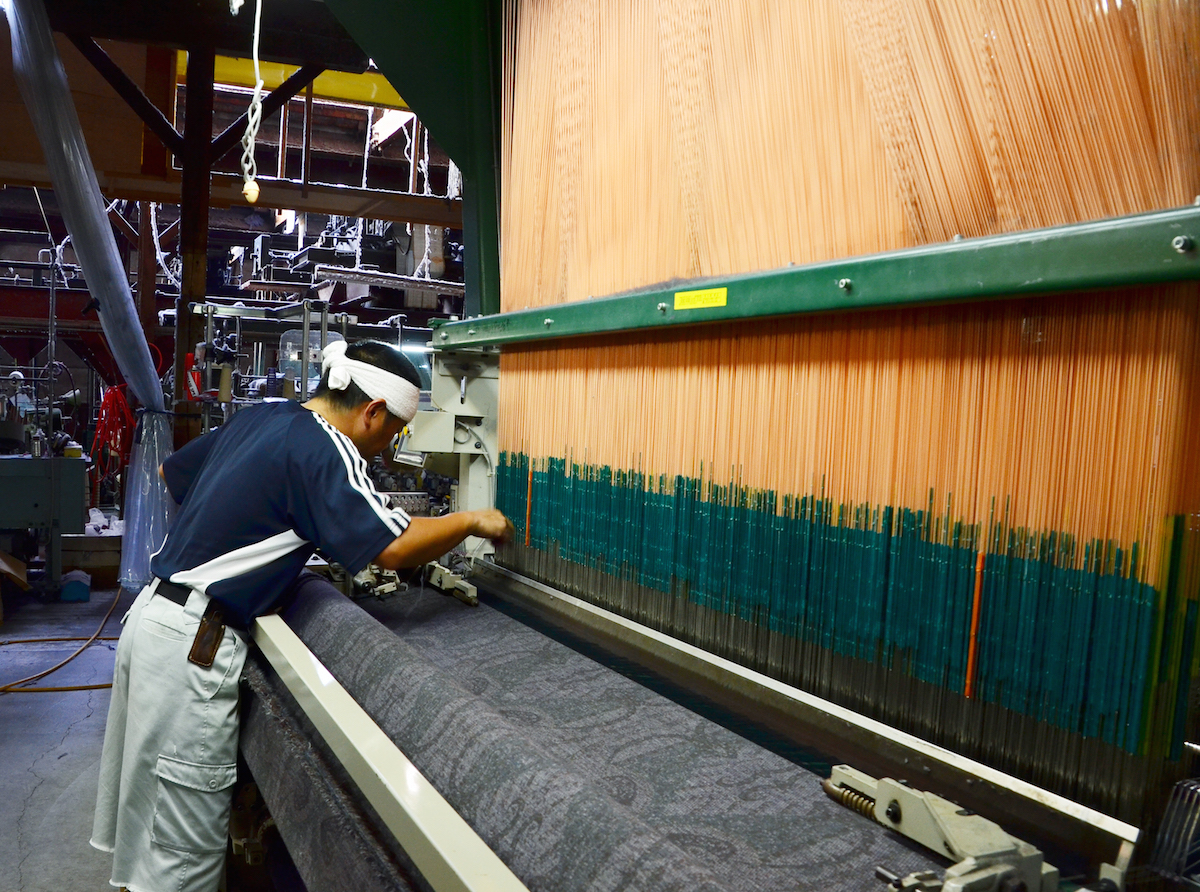
Endo manages the factory alone with her wife. He handles 11 looms all by himself.
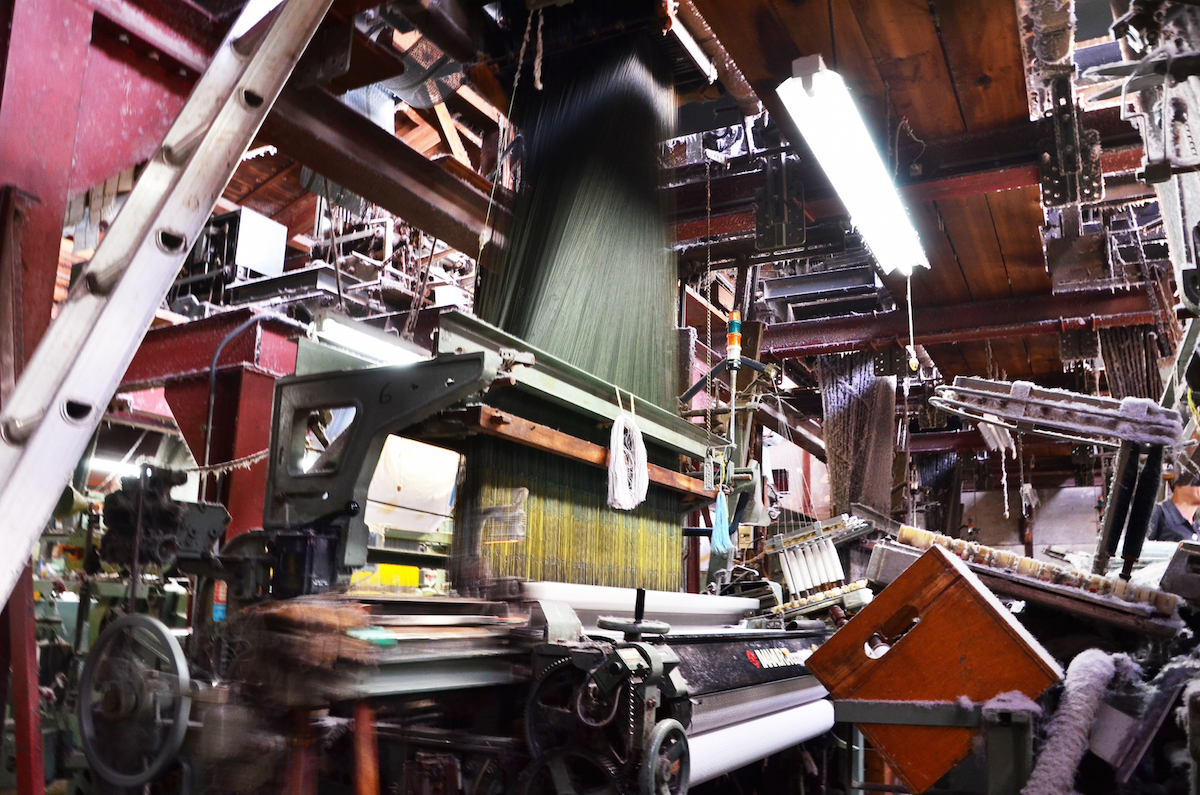
Inside Enmago, there are almost “antique” looms such as shuttle jacquard looms as well as latest models of looms.
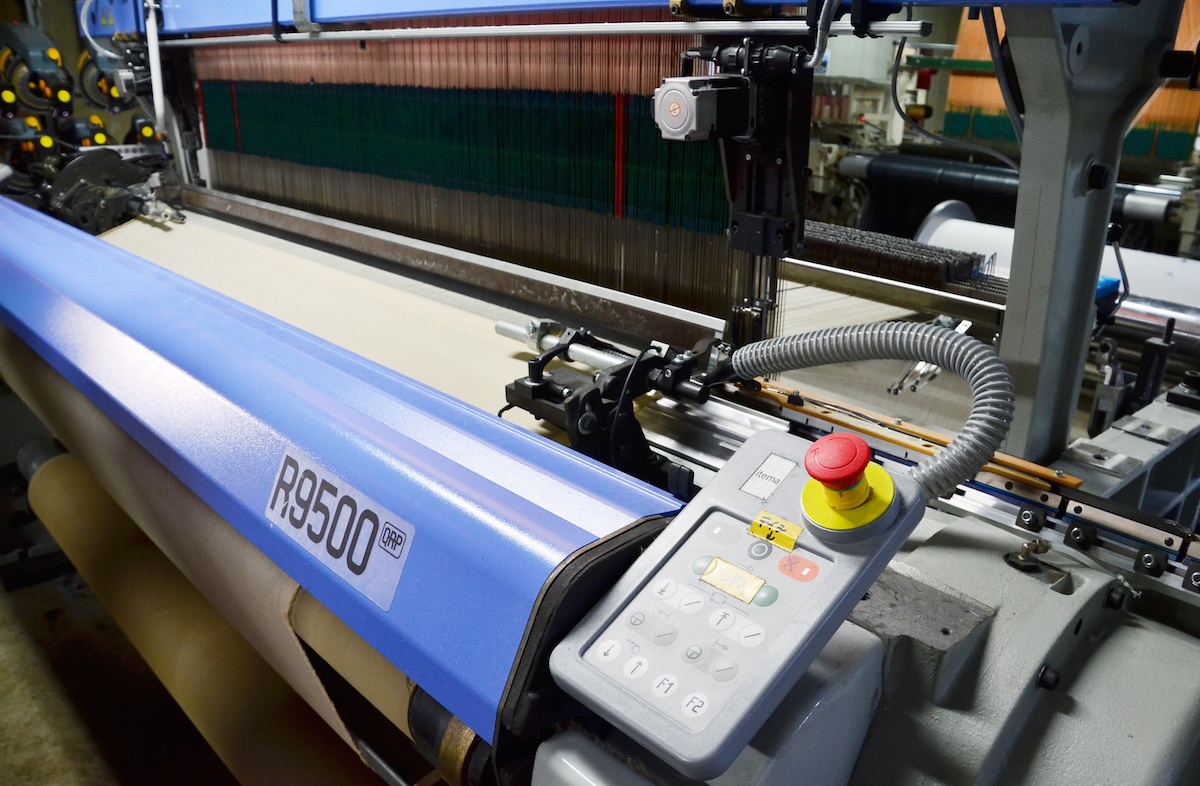
POLS textiles are woven with latest model of looms. With latest technology, sensitive any design could be delicately reflected.
People as “Weft”
Banshu textiles used to focus on striped and checkered fabric for men’s shirts. However, under the current CEO, Takao Maruyama, Maruman started to develop textiles for women’s apparel.
Maruyama says it was important to change the entire attitude in the area, including in his own company, to understand and meet the needs in women’s apparel. In order to achieve this, Maruman relays the comments and opinions obtained during sales, as a representative of the area, to the local factories.
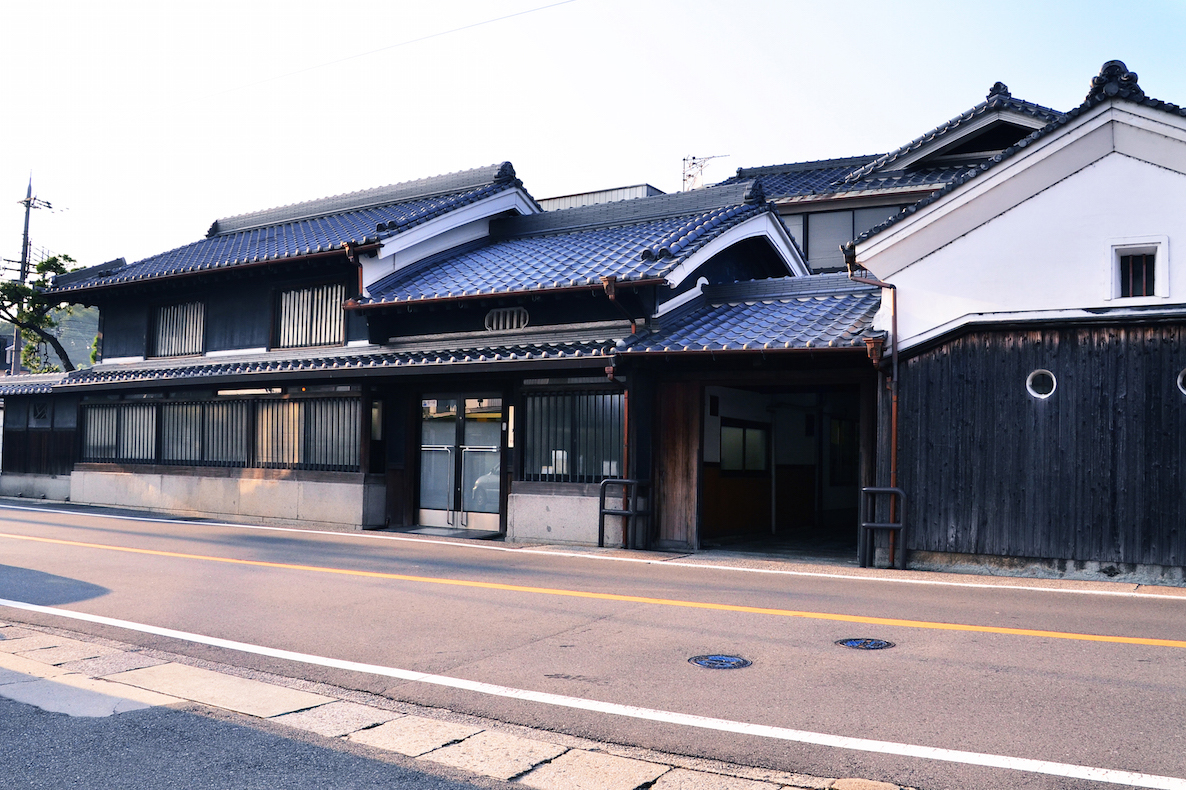
Facade of Maruman. Maruman, as local textile trader, works closely with local factories.
Therefore, in the front line of the production, the artisans must meet new challenges every day. However, the artisans have experience solving problems and coming up with new ideas on an ongoing basis.
The Banshu-ori Textile Industry Co-Operation has developed a new technique called the distressing process to create a unique touch by damaging the weft to make it wavy. The Muratoku Dyeing Company has been employing system engineers and developed their own method to speed up their process of yarn dyeing. They are fully aware of the need for strict control and speedy production these days.
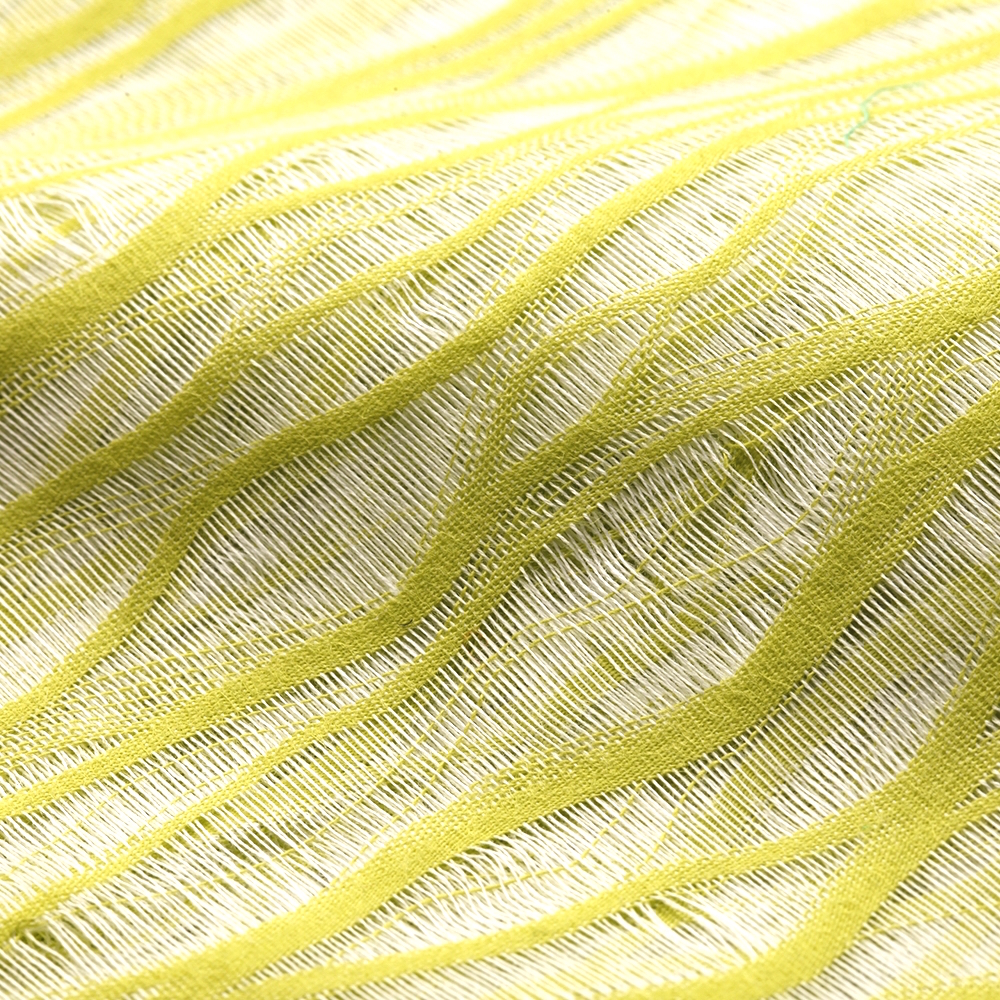
Award winning technique called “Crush Process” originally created by the Banshu-ori Textile Industry Co-Operation.
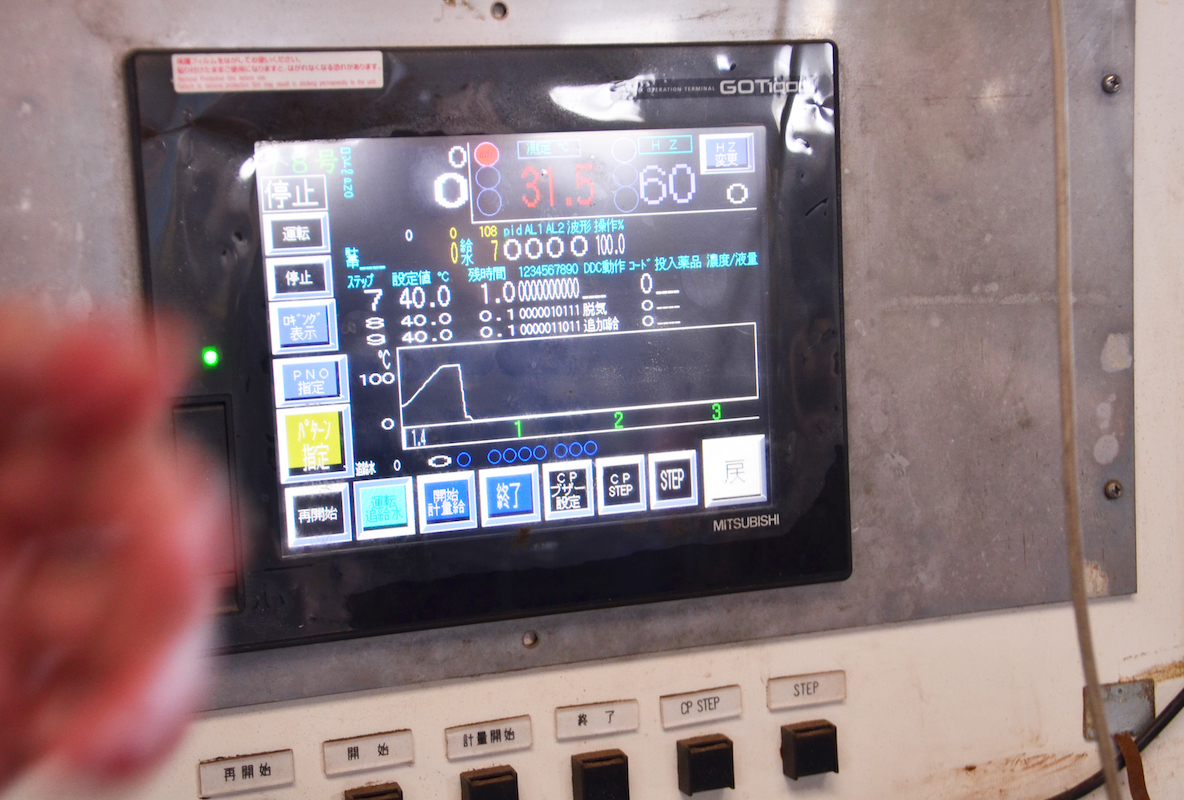
Muratoku Dyeing Company employs system engineers to optimize the process. By digitalizing, Muratoku tries to correspond to the quick and flexible orders due to recent market situation.
At last, the climate, and culture are the “warp” and the people who create the drama there are the “weft.” When you visit the city of Nishiwaki, you feel the infinite potential created by the combination of the area and the people, just like how POLS textiles are made.
(Translation by Akiko Ishige)