So, what is "homespun"?
Homespun refers to hand-spun and hand-woven fabrics, which originated in Scotland with sheep yarn. Woollen fabrics woven with this yarn are called tweed; however, today, the yarn that is used for tweed is machine made. Therefore, tweed does not necessarily mean homespun.
Homespun was first brought to Japan from the United Kingdom during the Meiji period, in the late 19th century, but the fabric was not widely used because of Japan’s lack of technology. After the First World War, wool imports could not keep up with the internal demand, and this led to a national policy to encourage keeping sheep domestically to be able to make yarn at home. As a result, people started to raise their own sheep and to make homespun products everywhere in Japan. This is how the country’s homespun industry began.
Because of the lack of materials and industrialisation during the post war era, the homespun industry declined rapidly. However, Iwate prefecture is still producing homespun. It is unclear why Iwate continues to be a producer of homespun, but many famous homespun companies still operate there, such as Nihon Homespun Corporation, Michinoku Akane Association, Nakamura Kobo (kobo is the Japanese word for factory or workshop), and Arikawa Kobo, which is introduced in this article.
When you touch the homespun made at Arikawa Kobo, you can tell right away that it has been made from high quality wool. This homespun also contains a lot of air, which makes its texture very soft. By using it again and again, you can get rid of its fluff and make it shiny. Eventually, it acquires a texture that looks like good cashmere and fits to your body. You can make this kind of homespun only by hand spinning and hand weaving. Seiko Ito, who succeed Arikawa Kobo, talks about her passion for the workshop and how she makes homespun diligently by hand.
Making clothes that improve with use over time
Arikawa Kobo‘s history overlaps with the history of homespun in Iwate prefecture. This kobo was established by Hironao Arikawa, the son of the first pupil of Oikawa Zenzo, who was the key person in Iwate’s homespun industry as well as a famous activist in the folk art movement.
Mr. Arikawa had an opinion based on Folk Art Movement. He wanted to make fabrics that become better as being used – fabrics you can use happily not only now but also decades and generations later. Arikawa Kobo is producing outfits that follow this idea.
At the Arikawa Kobo, chemical dye as well as natural dye is used to make the colours as durable as possible. When dying the homespun, they first dye the wool with 12 to 24 basic dyes. They then create colours by mixing and combing the coloured wool. For example, to create orange, they comb and spin red and yellow wool together. This is why homespun’s colours are deeper than single-dyed colours. In addition to reddish colours, multi-coloured homespun is also popular, says Ito.
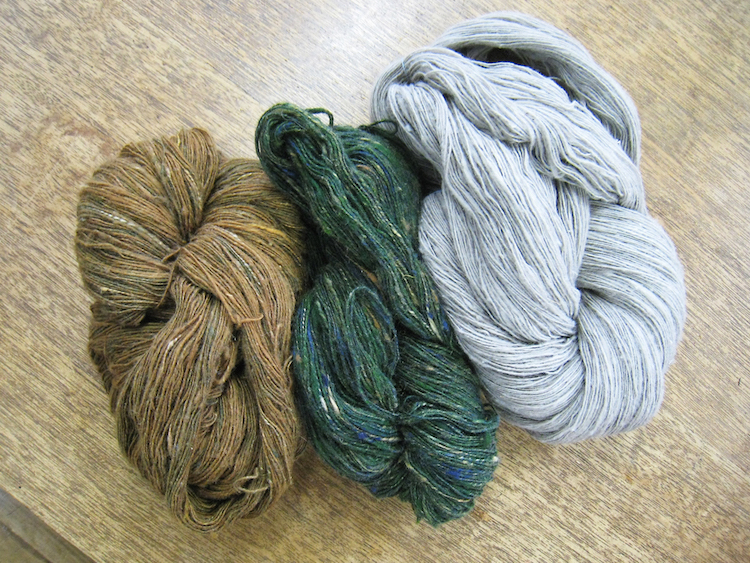
Yarns that is made by blending colours. (Photography: Courtesy of Arikawa Kobo)
With respect to spinning the yarn, Ito says that it takes her one month to make a coat. Clearly, it is nearly impossible to make a profit without using machines. However, she insists on producing handmade products because what she wants to do is pass down the whole homespun culture: making the textiles by hand spinning and hand weaving, cutting them one by one, seaming them, and then passing down the precious clothes for generations. Ito explains the tradition.
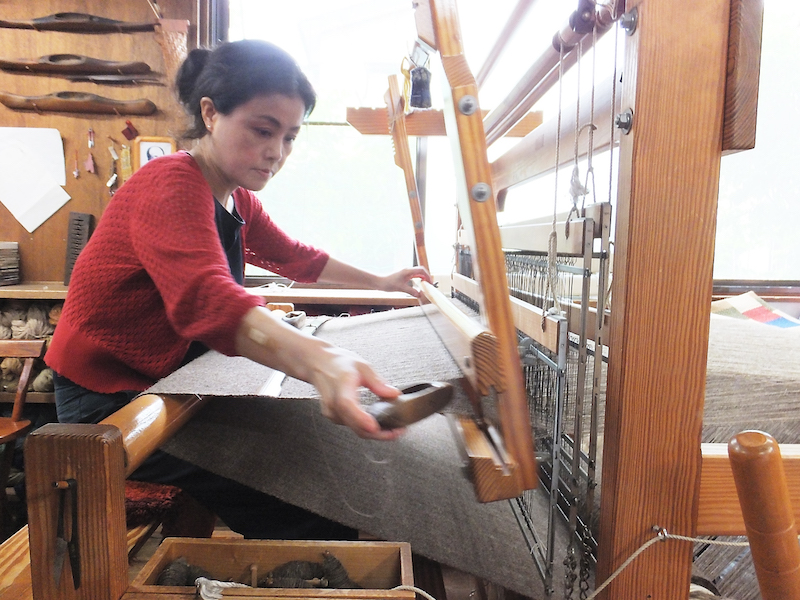
Once we were asked to produce textiles for a major company, for many of the people, it may be seen as a chance; however, we asked to be excused from it. We cannot make such amounts of textiles. Moreover, we did not want our textiles to be used by the company that would use our textile rather roughly to us.
People in Iwate admire homespun. They cannot buy them frequently as they are very expensive, so it is one of Iwate’s customs to order homespun wool jackets to celebrate their retirement. I’d like this culture to make each clothes with so much care to lasts long.
To make the never-ending job last
It was 24 years ago when Ito started an apprenticeship at the kobo simply because she lived nearby. At first she just wanted to learn about weaving, but she loves the work there so much that she took over operating the workshop in 2010:
Dyeing, spinning, weaving, and finishing up――every day is the same job, but it’s not exactly the same. Small things easily change the result in each process. I have been doing this job for years, but it never ends.
Today, Arikawa Kobo receives orders mainly for men’s coats. The company has fans among first-class tailors in Ginza, which is one of the most expensive areas in Tokyo, and holds exhibitions at a gallery there once every two years. However, homespun coats are not really common items since the number of tailors in Ginza is decreasing, and the coats cost as much as $2,500 because homespun textiles cost over $300 per meter. If this situation continued the homespun industry would decline, but Ito has an idea for a breakthrough:
Homespun has been secretly attracting attention in the fashion industry. I know this is very fortunate, but I must say that our industry needs to be known by more people. So I’d like to make more women’s products with designers who agree with our opinion and make coats with thorough care.
Ito’s favorite coat and jacket. (Photography: Courtesy of Arikawa Kobo)
Arikawa Kobo sells cotton and linen shawls as well as homespun scarves, which are easier to buy.
Many people may think beauty only lies in refined pieces by “artists”. However, it lies within the daily products made by artisans as well, and this beauty appears when people actually use them. Using such products helps to create culture, which will only serve to enhance the products even more. Arikawa Kobo is doing its job every day, diligently, by hand, so that this loop will never end.
(Translation by Akiko Ishige)