When you look closer at kapuwa’s colorful patterns, you can see that their prints are distributed in order. They are tidy, as if they were created by a machine, but the patterns are actually printed by hand. The boundaries between the colors are vague and the dyed colors are shaded, as if they were repeatedly painted using watercolors. I could feel different expressions on each fabric.
(* Picture taken by author)
The prints have a handmade warmth, while the artists’ accuracy and skills fascinate me! I visited Aiko Miyamoto, the founder and the designer of kapuwa to hear about the products’ craftsmanship.
kapuwa = Made in Jaipur
The kapuwa items are printed using a technique called Indian block print. This tradition originated in the state of Gujarat, in the western part of India. The print is still rooted in India, but its commercial hub is centered in a village in Jaipur.
Jaipur is called the “Pink City” because all the buildings in its old town area are painted in pink. kapuwa products are made in this known tourist spot where the residents live calm lives.
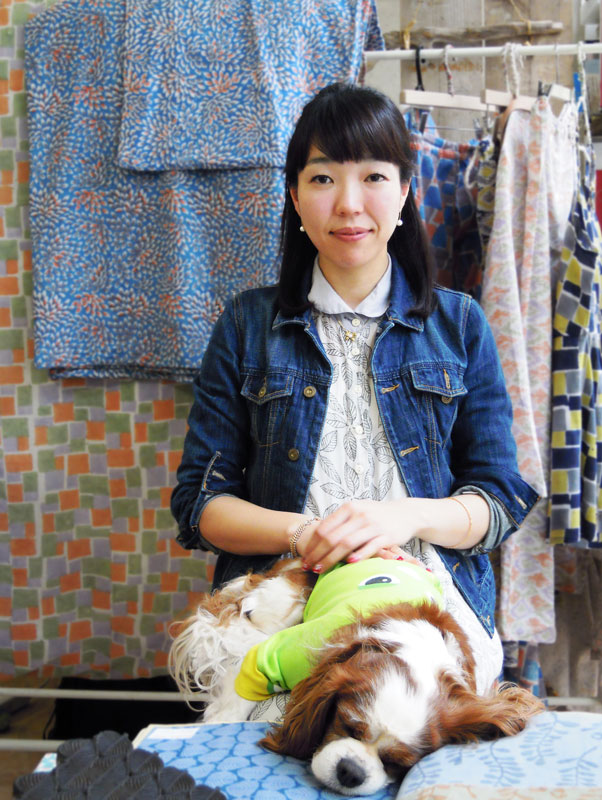
Aiko Miyamoto, the founder/designer of kapuwa (*Picture taken by the author)
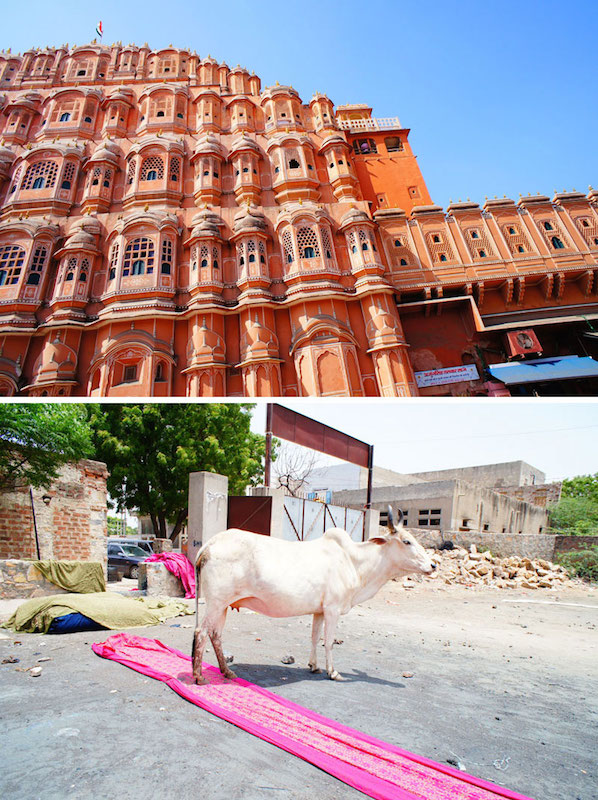
(Above)All the buildings, including the wall surrounding the city, is all colored pink.
(Bottom)Many animals are worshiped as god in India. Even if the animals are in the way, people never tries to move the animal, and calmly waits. It is one of the favorite Indian scenery for Miyamoto.
Making Wooden Blocks that Last 50 Years
First, Miyamoto draws the block print patterns that will be featured on the kapuwa creations.
I turn images into patterns with my PC. Block print requires woodblocks for each color, so I limit myself to four blocks to take that fact into account. Then I send it to the factory in Jaipur.
At this stage, Miyamoto often meets her business partner at the factory in Jaipur to choose the best cloth for the pattern.
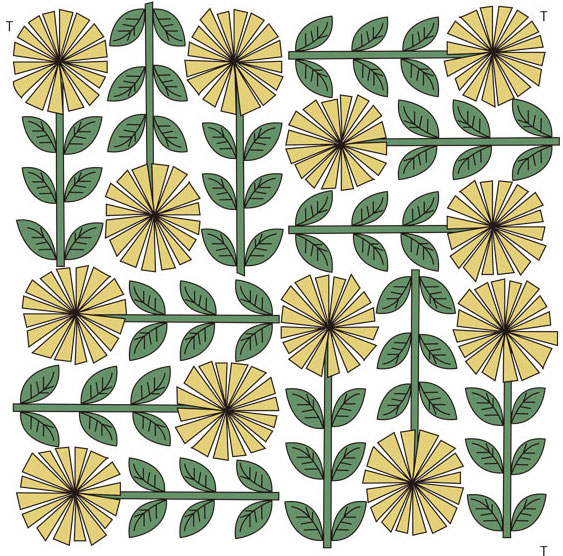
“Dandelion” design drawn by Miyamoto.
Then, artisans in Jaipur start to create the woodblocks based on her patterns. The woodblocks are made of a type of fern. This fern has an adequate weight and is soft enough to carve, which makes it ideal for the woodblocks. Miyamoto says that artisans take looking for the perfect piece of timber very seriously. These trees are limited resources, but “these woodblocks can be used again and again for 50 years without changing their carved lines.”
After copying each color part of the patterns onto woodblocks, the artisans start to carve them along the lines. It takes three to four days to copy and another three to four days to carve. In total, it takes about one week to create woodblocks for each color.
The blocks are then left in oil for a day to harden the wood.
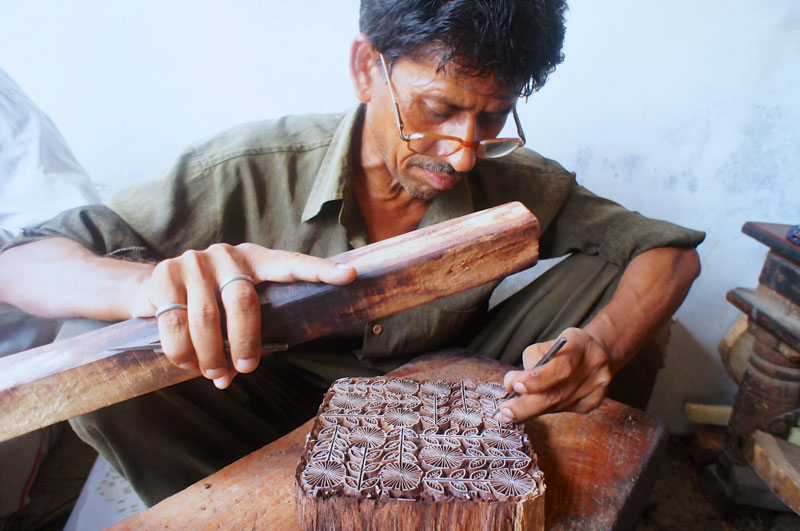
Artisan carving the design to a wooden block. Artisan can carve out any delicate thin expression into a line.
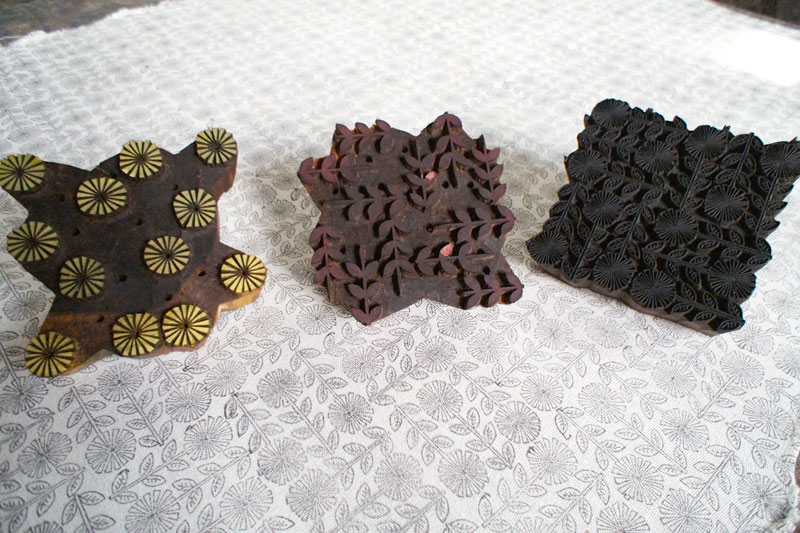
the Design, “Dandelion” is made of three blocks; from right to left, it is made of 1.Outline, 2. Leaves, and 3. Flower blocks.
kapuwa decided to use only four colors for one pattern, but we enjoy the potential within the limitation. We increase only one or two patterns per one collection. In addition, we change the combination of colors and cloths of patterns made in the past.
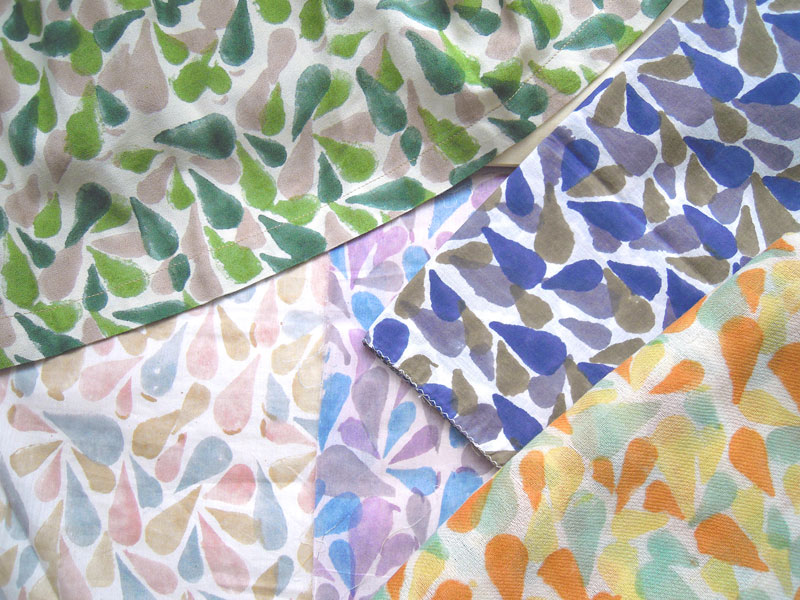
First pattern design with kapuwa. Every year it appears in kapuwa‘s collection, in variations of fabrics and colors. (*Picture taken by the author)
Artisans Read the Wind to Finish the Texture
Once the woodblocks are made, the artisans start to print on the cloth. The artisans each take one block and print in a row, as if they are chasing each other.
The blocks have small halls in them. Cotton soaked with color is put in the halls so that the colors last for a long time. The shading of the color seeps from the cotton, and the way the cloth sticks to the blocks, creating the unique expression of a block print.
The fabric roll can be up to 500 to 600 meters long, which makes it very difficult to dye by hand using the same color. To adjust the dye to the desired color, the artisans change the colors they blend together. They base their adjustments on the temperature, humidity, and number of daylight hours.
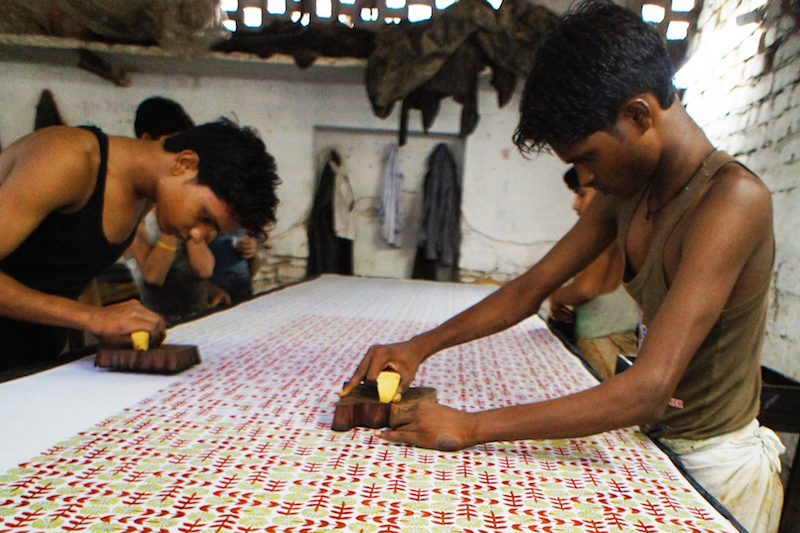
On the white plain fabric, there is only marks to know where to print the block. Although the colors are seemed to be different from what is designed, it will come out in the way it should be when the fabric dries.
In India, the weather changes a lot during one week. Our work depends on the weather, so all the artisans predict whether or not they should work. If it’s not sunny at five in the morning, they get a day off. Sometimes they say it will rain in the afternoon, even if it’s sunny in the morning. It always transpires to be true.
Design What the Fabric Wants to Be
Once the roll is finished, it is sent to Japan. Then, Miyamoto starts working on the design.
We don’t decide the themes for each collection, nor do we decide what to create from the start. When the printed fabrics arrive, I take time to seek what the fabric wants to be, how we can make the most of the characteristics of the fabric.
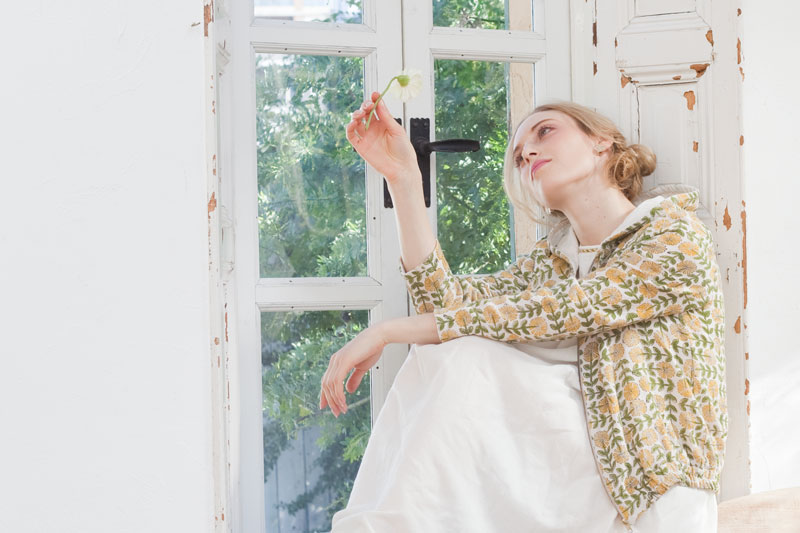
“Dandelion” Design drawn by Miyamoto now become a clothing, made by Jaipur artisans.(Parka: 9,800JPY, Dress: 12,000JPY, VAT excluded)
Miyamoto considers the factory’s technical level as well. Once she has finished creating the designs, they are cut out and sawn in Jaipur. Then, the kapuwa clothes are sent to Japan.
Special Place Found in Jaipur
kapuwa have continued to work with only one factory since the brand started.
However, before she started kapuwa, she had once worked with another different factory to improve her production process. That was when she realized that the current partner was special.
In the former factory, the owner was boasting about his luxury belongings, while the working area was underground and artisans spoke ill of the owner. That was when I realized that my current partner factory, where all the people in different positions can enjoy working, was special.

Artisans quietly keeps on printing in the room with comfortable atmosphere.
In their breezy and sunlit factory, everyone seems to enjoy working. You cannot take this for granted in India due to the caste system of Hinduism.
Her partner, the founder of the current factory, has learned skills and worked his way up the caste system, which made him caring and sympathetic toward his employees. Miyamoto says his care create the factory’s atmosphere, and is truly a rare case in India.
Now, it has been seven years since Miyamoto first met the factory in 2008 and five years since she started working with the factory. Miyamoto and the partner have built a deep, family-like relationship where she can even reveal her inner conflicts. The two partners’ relationship; professional, uncompromising attitudes; and commitment to not saying “No” to any order are core values at kapuwa.
Kapuwa’s growth with Jaipur
After looking at the kapuwa production process, I found that the partners respect each other and what they can do, and they move forward together.
When the factory develops new skills, kapuwa can increase the number of options that we can choose. I hope we can grow together without working too hard. I like the artisans who enjoy working.
The factory in Jaipur has grown so fast that there are at least five times the administration staff members compared to when Miyamoto first met them.
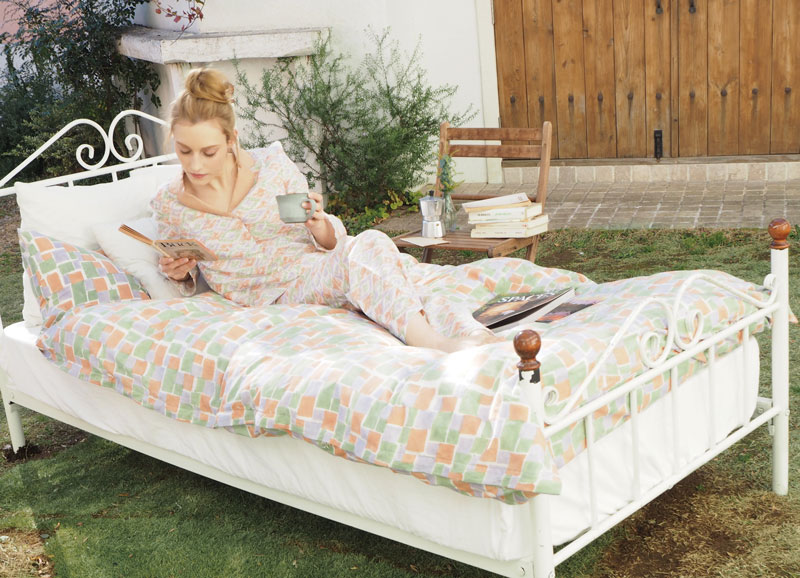
New homewear collection kapuwa home introduced 2015 Spring/Summer. (Pajamas: 9,200JPY, Bed Linen: 8,200JPY, Pillow Cover: 1,900JPY, VAT excluded)
On the other hand, kapuwa has become a company, and is expanding the potential of Indian block prints. Kapuwa Home, which focuses on relaxing goods, was introduced this May. Furthermore, it is even expected to participate in the Japan Expo in France.
I deeply appreciate the factory that helped us become a company. I’d like to keep passing on the block print technology in Jaipur as ‘Made in Jaipur’.
(Translation by Akiko Ishige)